Personal Injury
Below is a flavour of the areas where our services will be of use to clients. Click the title to expand or hide detail about each section.
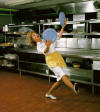
Slips, trips and falls account for more than 30% of all major non-fatal injuries reported to the Health & Safety Executive, by far the most common cause of reported non-fatal major injuries and up to 20% of over-3-day injuries. The annual cost of these accidents to society is estimated to be as much as £750 million with £300 million directly attributable to costs to employers.
The presently accepted method for measuring slip resistance incorporates the use of two instruments, the Stanley type pendulum skid tester and a pocket sized meter for the measurement of surface roughness. We have the instrumentation and can interpret the results to provide an assessment of floor surface slipping characteristics both in the dry condition and with any relevant contamination.
More than a quarter of the accidents reported to the HSE each year are associated with manual handling - the transporting or supporting of loads by hand or by bodily force. While fatal manual handling accidents are rare, accidents resulting in a major injury such as a fractured arm or a significant back injury are more common, accounting for nearly 10% of all major injuries reported in 1996/1997. The vast majority of reported manual handling accidents result in over-3-day injury, most commonly a sprain or strain, often of the back. The Manual Handling Operations Regulations 1992 apply to all manual handling operations which involve a risk of injury. We are able to investigate causes of manual handling accidents of all types, we have specialised equipment for measuring loads, whether lifting, pushing or pulling, and can interpret the results in relation to the legislation.
Industrial Disease Investigation
The musculoskeletal system is well suited to producing repeated motions at low force levels. However undesirable forces may be imposed on muscles, tendons and joints by some job demands and working practices. Such stresses are uusually within the physical capability or strength of the tissues, provided the forces are of short duration and rest periods are adequate. Prolonged tissue loading caused by static posture or performance of very frequent exertions can however be harmful. Such conditions as carpal tunnel syndrome, de Quervains disease, epicondylitis, tenosynovitis, shoulder capsulitis and others may be caused by work activities.
New guidance from the Health & Safety Executive recommends a framework for the management of upper limb disorder risks. We have been undertaking investigations of upper limb disorders (repetitive strain injuries) since 1979 and have considerable experience in this field. Investigations usually entail close examination of the work process, which is video filmed and can be observed in slow motion to identify whether or not harmful motions, gripping actions or similar arise in the activity. Our Engineers have frequently given evidence in High Court in this particular field.
More than a quarter of the accidents reported to the HSE each year are associated with manual handling - the transporting or supporting of loads by hand or by bodily force. While fatal manual handling accidents are rare, accidents resulting in a major injury such as a fractured arm or a significant back injury are more common, accounting for nearly 10% of all major injuries reported in 1996/1997. The vast majority of reported manual handling accidents result in over-3-day injury, most commonly a sprain or strain, often of the back. The Manual Handling Operations Regulations 1992 apply to all manual handling operations which involve a risk of injury. We are able to investigate causes of manual handling accidents of all types, we have specialised equipment for measuring loads, whether lifting, pushing or pulling, and can interpret the results in relation to the legislation.
Display screen equipment which include traditional work station computers, are required to meet a certain standard as are the work stations in which they are installed. The Health & Safety (Display Screen Equipment) Regulations 1992 list the requirements for the analysis of work stations, the minimum for work stations, the daily routine of the users, eyesight checks and the provision of information and training. In the absence of appropriate equipment and work routine, the main hazards associated with display screen equipment include upper limb pains, neck discomfort, eye problems, fatigue and stress, as well as a suggestion they may cause other problems associated with epilepsy, facial dermatitis and there may be effects on pregnant women.
We are able to examine work stations and report on the extent to which they satisfy the requirements enumerated by the Regulations, and provide a view on workload, provision of breaks and similar criteria and provide opinion as to whether equipment is of the correct design or individual workers are being overworked.
Industrial deafness (noise) cases and claims associated with Vibration White Finger (VWF) and Whole Body Vibration have several things in common, not least that the majority involve a prolonged period of exposure with that exposure counted in years rather than days.
We are equipped with the instrumentation necessary to assess the exposure levels to which workers are subjected and have experience of how, using all available data, earlier years of exposure can be taken into account when preparing a case. The progressive tightening of Standards (“Action Levels”) in Directives from Brussels is likely to give rise to an increase in the number of claims coming forward.
Industrial deafness (noise) cases and claims associated with Vibration White Finger (VWF) and Whole Body Vibration have several things in common, not least that the majority involve a prolonged period of exposure with that exposure counted in years rather than days.
We are equipped with the instrumentation necessary to assess the exposure levels to which workers are subjected and have experience of how, using all available data, earlier years of exposure can be taken into account when preparing a case. The progressive tightening of Standards (“Action Levels”) in Directives from Brussels is likely to give rise to an increase in the number of claims coming forward.
There is increasing awareness of diseases arising from exposure to substances hazardous to health. These are generally industrial chemicals, or formulations, but occasionally comprise biological agents. The diseases include irritant or sensitisation dermatitis, asthma and RADS (reactive airways dysfunction syndrome), pneumoconiosis and acute or chronic toxic effects characteristic of specific chemical exposures e.g. to solvents, metalworking fluids, metals, mineral oils, carbon monoxide, acidic substances. Since 1989, with certain exceptions (e.g. lead, asbestos), these substances have been subject to successive Control of Substances Hazardous to Health Regulations. We have extensive knowledge of the risks and of appropriate measures for their prevention or control, and monitoring.
Understanding of the role of occupational carcinogens is continually being up-dated. We have experience in advising on the risks, and on claims which may arise e.g. involving dyestuffs, mineral oils, rubber chemicals, leather/hardwood dusts, nitrosamines (see also asbestos).
The commonest asbestos-related diseases are asbestosis, pleural plaques or diffuse pleural thickening, lung cancer, and mesothelioma. For over 30 years we have investigated numerous claims arising from occupational or para-occupational (neighbourhood) exposures to asbestos dust. Many exposures pre-date the Asbestos Regulations 1969 and were not covered by the 1931 Regulations. Relevant dates of knowledge have been established from detailed literature reviews.
Claimants tend to have numerous employments. Whilst inspections have sometimes been possible, with the time scale involved (e.g. with a latency period of over 10 years with mesothelioma cases) workplaces generally cease to exist or have been substantially modified. Reliance therefore has to be placed upon experience of past working conditions in the industries, likely levels of dust exposures, and contemporaneous precautionary measures in order to assess the relevance of each employment. This is necessary to estimate the probable, if any, contribution of each period of exposure to contraction of the specific disease.
Many accidents occur at work through failure to provide suitable work equipment and/or failure to maintain such equipment or through failure to train employees in the correct use of such equipment. The Provision and Use of Work Regulations and Approved Code of Practice usually apply to such accidents. Our engineers have wide knowledge of the appropriate equipment which should be provided and used in industrial situations and can isolate the causes of accidents arising there from, including any failure to provide guarding for dangerous parts.
There is a duty under the Regulations to provide a workplace which will not have adverse effects on health and safety. There are requirements relating to ventilation, temperature, lighting, cleanliness, seating, floors, traffic routes, the provision of clean drinking water and much more. With our wide experience of health and safety matters, we are able to interpret the law, provide assessment of workplaces, surveys and interpret the law when an accident occurs.
Every year many construction site workers are killed or injured as a result of their work; others suffer ill health such as dermatitis, occupational deafness or asbestosis. The hazards are not, however, restricted to those working on sites. Children and other members of the public are also killed or injured because construction activities have not been adequately controlled. We have particular expertise in the investigation of all aspects of construction site health and safety. Civil Engineers within the practice are also able to comment on structural problems and contractual disputes.
The causes of process or materials-related fires (e.g. those involving liquefied petroleum gas, natural gas, flammable or highly flammable liquid) are not always readily apparent. We have detailed, science-based knowledge of such incidents, their investigation, the potential effects of exposure to combustion products; and the precautions required in industry.
These also cover explosions entailing combustion e.g. in furnaces, buildings or with gas cylinders. Also included are those due to chemical reactions, failures of pressure systems (Pressure System Safety Regulations 2000), rupture of glass or plastic containers or rapid steam generation as encompassed e.g. by the Work Equipment Regulations.
To search our areas of expertise, please click here.